BRD chooses ULMA Packaging to upgrade its production plant
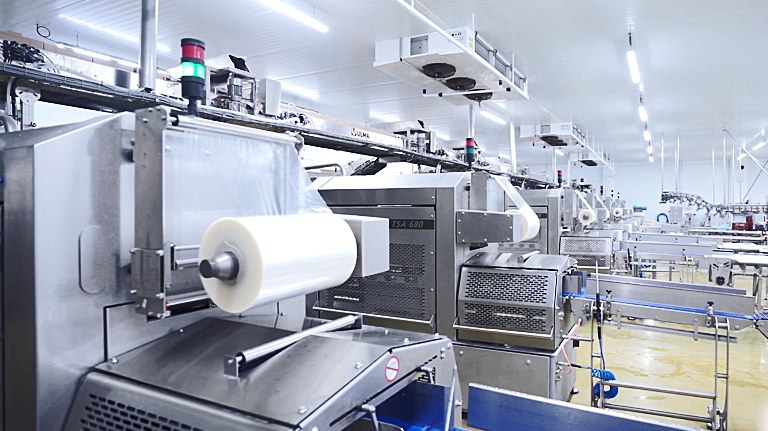
The Bernard Royal Dauphiné brand was created in 2001. A subsidiary of the Terrena group through the Galliance (Loire-Atlantique) subdivision, Bernard Royal is based in the centre of Drôme. Its main activity is the butchering, processing and packaging of poultry. Bernard Royal Dauphiné currently employees 170 people and achieved a turnover of 60 million euros in 2017.
The firm belongs to Terrena's poultry farmer sector, one of the largest cooperatives in France, whose policies are aimed at strengthening ties between producers and consumers. To stand out from its competitors, BRD adopted a regionalised supply strategy, selling the chickens that it rears within a 50 km radius and feeding them with regional produce. They are sold within the Lyon-Perpignan-Monaco triangle, where there are a total of 22 million consumers.
Construction of the new butchering plant began in 2017 and it occupies 2,500 m². Seven TSA 680 traysealer lines and an ULMA Packaging thermoforming machine were installed in the facility, making it possible to simultaneously package chicken wings, fillets and thighs on all of the production lines, achieving an output of 5300 chickens/hour. The system allows it to perform traysealing and modified atmosphere packaging. The trays are packed automatically thanks to the 7 ULMA Packaging robots. Thanks to making that investment, BRD has doubled its output and it is now able to cut up 270,000 chickens per week.
Set up in record time
The main challenge faced by ULMA Packaging when performing this installation was being able to set up all 7 packaging lines in record time. In fact, production in the old plant was stopped on a Friday and the new one had to start production on the following Monday. For this purpose, the whole installation was shown to the customer in Oñati, in ULMA Packaging's facilities. The new machinery was tested there in the presence of technicians from ULMA Packaging Spain, ULMA Packaging France and specialised personnel from BRD. When the new equipment was installed in the factory, output rose very quickly and the target speed that had been set for the new installation was achieved in less than two weeks.
When upgrading the plant, the customer needed to continue producing at full capacity while replacing the installation and also using the same staff. To make this possible, ULMA Packaging's teams made the commitment to install the lines as quickly as possible and to assist in setting them up, as well as providing them with the necessary training to operate the new machines.
Turnkey solution
One of the strengths of this project was that ULMA Packaging offered the customer a complete solution, while also bringing its experience from other installations previously completed in the sector. ULMA Packaging's technical teams listened to the customer, so they were able to offer a turnkey solution that would meet the established requirements.
After two years in operation, the project's initial productivity targets have been met. The working conditions have been improved, thus reducing safety risks and increasing productivity to the levels required by the customer. This project, based on trust and the strong relationship that has been built between ULMA Packaging and BRD, has been a success.