Day in the life: Packaging Service Solutions
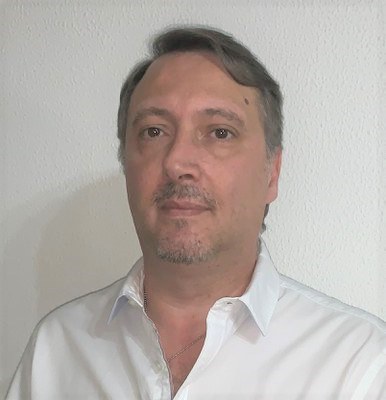
Joe has been a fixture in the UK’s packaging industry since arriving from Portugal in 2004. From his time working as a machine minder for a poultry company in Norwich, he knew that he wanted to progress further within the UK packaging industry. It was then in 2014 that an opportunity with ULMA Packaging UK arose for the position of service technician in Lincolnshire and Norfolk. By 2017, his passion for the industry resulted in his swift promotion to area service manager.
Now with over a decade of packaging machinery experience under his belt, Joe is prominently placed within ULMA’s servicing team and knows exactly how to provide the best servicing solutions for clients.
A hands-on approach
Much of Joe’s time is spent managing packaging machinery service and repair needs in the Lincolnshire and Norfolk area. Working within a flexible UK team, Joe is able to identify service issues and quickly assess the needs of the customer before deploying the best service engineer for the job.
Joe, explains: “The day begins with me communicating with the office to acknowledge new appointments with customers and to check the availability of spare parts for the machinery that the team and I will be working on that day. From there, we’ll ensure that the customer is visited at their earliest convenience to repair or service their packaging machine.”
Given the vast array of packaging machinery types available, coupled with the intricacies of each, no one day is the same. Joe, comments: “With over 70 different types of machine variants available, some with bespoke mechanisms and programming to be able to meet the packaging demands of the client, each day can be very different to the next.”
Engineers typically deal with one customer per day in order to allocate the right amount of time and expertise to resolve issues promptly. However, being able to react quickly and change service schedules across the course of a day is also a must, Joe said: “Excellent organisational skills are needed to prioritise and deal with enquires that require an immediate response. I will rearrange the services that we had planned for the day, so that the right technician can be sent out to the job.”
Proactive Management
ULMA Packaging UK has a reputation for product development, so it is imperative that the service team keep up to date with the latest technologies in order to offer the very best service and upgrade solutions when required.
Joe, explains: “ULMA prides itself on pioneering innovative packaging machinery solutions, in turn this means that the service side of the business needs to match this. New technologies and changes in software present a big challenge and it is not uncommon for a machine to be released, only for the software and technology to have been upgraded months later. Joe, continues: “To stay one step-ahead of software changes, regular training and updating of our team’s skills is an important part of the job.”
People Vs Machines
Reflecting on how important customer service is, Joe feels that to be a service engineer in the field requires a special type of person. One who enjoys working with people to get under the skin of the business, as well as having the right technical knowledge and problem-solving skills to understand the machines.
Joe, comments: “I try to put myself in the shoes of the customer always, because ultimately, no machinery means that they are not making money. It is this ability to empathise with the customers that I believe creates a strong and lasting relationship with those in my management area. Ultimately, I enjoy seeing the customer happy and their machinery working reliably.”