Enhance efficiency with thermoforming
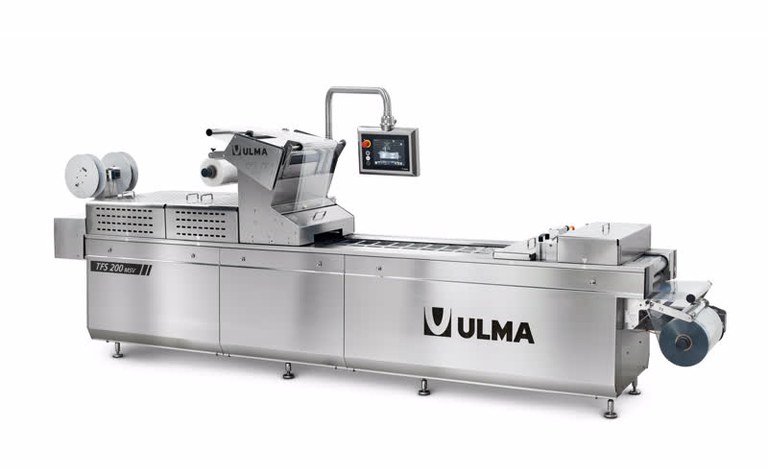
When it comes to packaging, the need to be conscious of consumer demands for sustainable materials in a highly competitive marketplace, means manufacturers are constantly looking at how to achieve optimum efficiency throughout the packaging process.
Thermoforming is already widely considered to be more energy efficient and environmentally-friendly than many alternative methods. By creating a process that is truly efficient from the top-down, organisations can reap the rewards in terms of increased productivity and savings; all of which helps secure a competitive edge. Here are four key ways thermoforming can help manufacturers achieve optimum efficiency.
1: Remove transportation
Starting at the top of the supply chain and considering the transportation of packaging material, there is a huge cost saving that can be made here. Due to the nature of thermoforming, the finished package is fully formed on the machine from a roll of stock material and created on demand. Unlike pre-formed tray lidding processes where the empty packages have to endure being transported to the manufacturing facility, the thermoform process creates an opportunity for processors to use lighter gauge materials to create the package. This reduces cost and complexity in the upstream logistics meaning organisations can focus their efforts on handling the final pack, helping to dramatically reduce costs, as well as positively impacting the environment.
2: Address inefficiencies in the process
To remain competitive, manufacturers must adapt and make changes where necessary. Some may prefer to queue the product in the process, however this is incredibly inefficient. Using a thermoforming method can offer manufacturers the opportunity to look at how the packing format can be integrated into the process and drive positive change throughout the production line. This not only helps to improve precision but also ensures every step is optimised.
3: Target waste at the processing stage
All packaging processors generate some degree of loss in raw material, over a production period this could equate to an excessive amount. It also costs to remove such waste from the business’s premises. However, ULMA has developed a reduced scrap machine that helps manufacturers save, in terms of material waste and disposal costs. The reduced scrap feature on the TFS407R uses a narrower reel of film than those used by equivalent standard machines, which can reduce waste by up to 40 percent. Everything that is processed on the machine is automated – helping to improve productivity.
4: Greater appeal for the end-user
With thermoformer machines, there is more opportunity to experiment with new materials and increase packaging recyclability. For example, the TFS 200 MSV is compatible with both recyclable film and paper board as well. This makes the machine the ideal packaging solution for food processors looking for more sustainable ways of protecting, transporting and displaying produce from the point of harvesting or manufacture to retail outlets. With public opinion driving the need to reduce single use plastics, especially in the case of product packaging, it will be simple touches like this that help give manufacturers a competitive edge.
Whether a manufacturer is looking to achieve cost savings or become more environmentally-friendly, thermoforming packaging could really transform the whole process.