Regular packaging machinery maintenance key to business performance
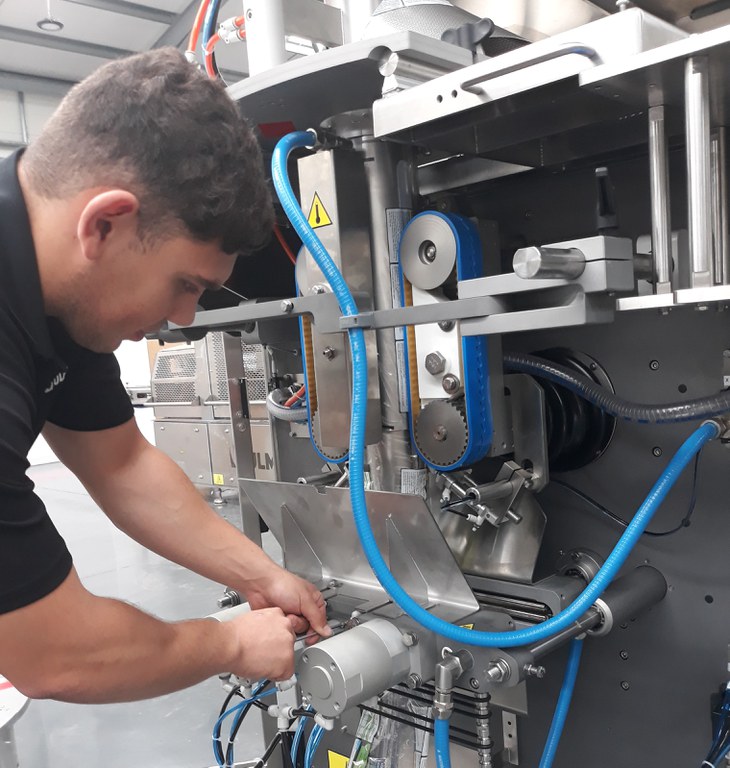
Unplanned downtime can have pronounced financial, logistical and operational implications on a packaging line, especially in harsh operating environments, or those working with high volume batch sizes.
ULMA Packaging is encouraging companies to adopt best practice in maintenance by not only taking out Planned Preventative Maintenance (PPM) plans, but by regularly checking and cleaning core mechanical parts throughout the year.
Taking the time to routinely check key operational parameters such as the positioning, pressure and condition of rollers and jaws outside of planned maintenance can easily prevent problems with sealing, cutting and other minor malfunctions; and ensure the highest quality standards are maintained between services.
Likewise, making the time to ensure that sealing, roller and jaw temperatures are appropriately set and maintained; and that the film reel is correctly centred, will also help to maximise operational performance.
Dave Berriman, technical manager at ULMA Packaging, comments: “It goes without saying that prevention is always better than the cure, and those customers who have taken out planned service and maintenance contracts will naturally reduce the volume of production downtime due to unforeseen breakdowns. However, just as you would undertake basic maintenance tasks on a car in between planned services and MOTs, so too should you apply this thinking to industrial process equipment, including packaging machines.
“By routinely checking simple things such as the security of key wired connections, as well as whether rollers and cutters are correctly cleaned and calibrated, you can keep your equipment running at maximum operational capacity for longer.”
He continues: “ULMA’s service technicians have a wealth of knowledge accrued over many years within the packaging industry, and regularly travel the length and breadth of the country as part of planned maintenance visits to keep our customers’ machinery operating at maximum capacity. However, going that extra mile to keep on top of smaller jobs between visits could prove to be invaluable in not only limiting downtime, but also ensuring quality is maintained throughout the year.”