Sustainable packaging without sacrificing efficiency
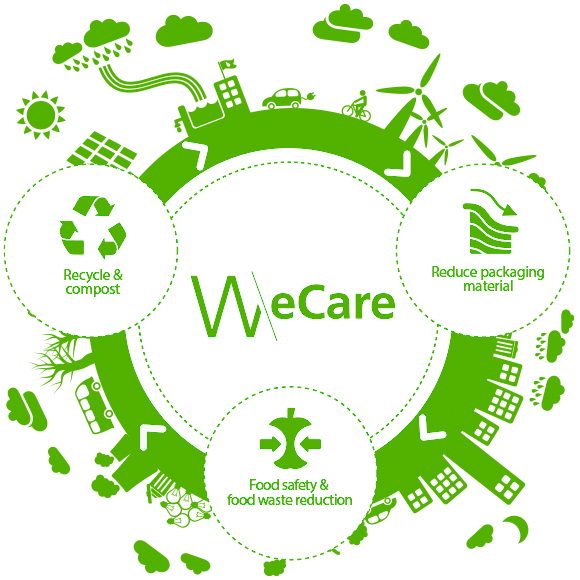
Energy prices and supply chain delay concerns dominated the news agenda in 2022, yet sustainability remains a key concern for the food industry. Indeed, environmental legislation has become stricter over last year, with the Plastic Packaging Tax’s rollout in April 2022 charging organisations for using plastic packaging with less than 30% recycled content.
The food manufacturing industry must therefore address this growing concern. But to do so, it needs to work closely with experienced packaging machinery providers. This is especially true considering the need to ensure efficiency, productivity and consistency in a business landscape that was already challenging prior to the implementation of more sustainable practices.
Thermoformers
There have been great strides in thermoforming technology to ensure less material wastage. Specifically, there has been a major focus on scrap reduction around the edge of packages, with pack width reduction a key priority. In particular, the pack skeleton has been highlighted as an area in which economies can be made.
ULMA and material provider SAC have made progress in this area, resulting in the development of the TFS 407R thermoforming machine. This model allows a vacuum to be created through specially designed air holes in the bottom film as part of Ulma’s Reduced Scrap innovation. The skin’s top and bottom webs further optimise vacuum quality while also allowing for a 12% cycle increase compared to standard Darfresh and skin machines. Crucially, this increased performance is matched by improvements in sustainability, with up to 40% skin/scrap reduction from individual packs, and up to 4% film reduction. Similarly, the TFS 216 provides a zero-scrap solution, reducing waste even further.
Additionally, machinery suppliers are continuously working on solutions that are compatible with multiple materials to cut down on plastic use. Two innovations developed under the #ULMAweCare initiative, LeafSkin and LeafMap are clear examples of this. Compatible with thermoformers and using a recyclable flat carboard tray, each pack design incorporates an ‘easy open’ corner to remove the lid and a ‘recycling’ corner to separate the different materials for whole and sliced items respectively. Consequently, material separation and recycling processes are made much easier, allowing for plastic reductions of up to 80%.
Traysealers
Advances have also been made with traysealing technology to enhance sustainability while ensuring machinery remains durable, practical and high-performing. Vital to this is material use, especially as food manufacturers look to cut down on plastic. Pack integrity has traditionally been an obstacle for sustainable practices, with non-plastic mediums often subject to staining and impairment when used in food applications.
With this in mind, barrier films are a viable way to implement eco-friendly mediums without compromise risks. Put inside the tray as part of the packaging process, these allow for large plastic reduction while providing another protective layer, increasing durability. As such, food manufacturers and processors using traysealers can greatly improve operational sustainability.
Ulma’s TSA range, for instance, is compatible with this technology, alongside various materials, including polyester, carton, cardboard and aluminium. As well as also being compatible with LeafSkin and LeafMap, machinery from this line can be scaled up from the TSA 540 to the TSA 1200 depending on volumes being packaged, allowing companies to amplify their sustainability credentials.
Verticals
For organisations using vertical bagging solutions to package food, sustainability improvements can lie in improving the pack-fill process. As a result, packaging machinery providers have ways to reduce secondary packaging used, with air extraction technology holding particular appeal. Previously, air was removed from bags by adding perforations. However, in the food industry, this hole-punching method can allow potential contaminants to ingress into the pack – even through very small holes – and humidity loss.
Technologies have since been developed to remedy this, with Ulma creating the tight bag extraction method. Allowing for adjustable volume, the innovation uses a patented jaw arrangement in the packaging machine’s cross-seal area, resulting in smaller, fully closed bags and more units able to be packed into crates and pallets. As a result, transport emissions are reduced while supply chain efficiency is also increased, with product damage also less likely as it has less room to move.
Further sustainability and efficiency benefits can be found in packaging of loose leaves and herbs. These delicate and lightweight products can present unique challenges, including blockages in the forming tube, and contamination from leaves being pulled into the seal. Due to this, new solutions have been developed addressing these concerns while also reducing packaging film use, including Ulma’s VenturiTM System.
Running 15-20% faster than a standard vertical line, the technology pulls products down to the bottom of the bag via a vacuum, rather than through previously used gravity-based methods, eliminating seal, blockage and other movement-related issues. This improvement is also markedly greater compared with horizontal flow wrappers traditionally used to packaging leaves and herbs, working 25-50% quicker. Moreover, accelerating products to the bottom of the bag reduces pack size by 15% due to reducing the amount of headspace required, resulting in less film used. Vertical packaging machines can also be recalibrated to run at a higher pressure and reoriented with different approach angles, reducing creasing and ripping risks for paper packaging.
Flow wrappers
This benefit also applies to horizontal flow wrappers, which can be adapted with paper kits to mitigate tearing concerns by providing specialist feeding systems on the machine to relieve stress points for the material. It is vitally important that specifiers at food manufacturers consult with packaging experts ahead of doing so, to ensure the correct machinery is identified and purchased.
Companies are also increasingly choosing mono-material packaging films due to their increased recyclability compared to traditional packs. However, this presents issues around pack sealing on flow wrappers, as options such as mono-PP and mono-PE laminates have narrower optimal sealing temperature ranges than conventional materials. As such, there has been increased focus on systems that can improve the process’s accuracy and calibration on packaging machines, leading to solutions such as Ulma’s Better-Seal.
Developed as part of the #ULMAweCare strategy, innovations such as Better-Seal will be key to moving the food industry away from multi-layer flexible packaging as a protective barrier. By instead selecting options where 90-95% of the packaging consists of a single material, the transition to a sustainable circular economy can be accelerated. Crucially, via materials such as mono-PE, the advantages of traditional materials – physical flexibility, design versatility and high performance protecting products – will not be lost.
It is for this reason that Ulma’s flow wrapper range is compatible with the Better-Seal system and paper kits, providing excellent performance and hygiene credentials alongside these sustainability benefits. Additionally, these flow wrappers are compatible with automatic feed systems, allowing organisations to exponentially improve operational sustainability by increasing packaged product volumes.
Automation
Automation offers another route of markedly improving the impact of sustainable operations, with labour shortages resulting in more food manufacturers exploring secondary packaging options for product loading into crates, cases or baskets. Implementing these technologies on the packaging line can have indirect, secondary environmental benefits, as sustainable practices and solutions previously discussed can run in a more efficient manner.
Consequently, this boost in productivity further increases any previous green benefits, including material reduction and replacing traditional mediums with more eco-friendly alternatives. Alongside this, removing skilled workers from tasks that can be automated allows for reallocation elsewhere in the factory for greater impact, with the potential to make operations more efficient through smarter working utilising a higher skilled workforce, and negating any issues related to labour shortages.
Next steps
In conclusion, the need for food manufacturers to make operations more sustainable has become extremely pressing. Most of the factory floor can be adapted with this goal in mind, with packaging systems and processes a standout area where implementing greener practices can have a major effect.
Of all suppliers in the packaging industry, Ulma Packaging (Ulma) stands out as the provider with the widest variety of machinery suiting all applications and products. With over 60 years’ experience and representation in over 130 countries, Ulma offers a unique proposition as a Spanish based co-operative. Additionally, its ability to provide machinery and specialist consultancy across all sectors, including food manufacturing, means the organisation is well-placed to tackle sustainability concerns, primarily through its sustainability initiative, #ULMAweCare.
It is therefore advised organisations get in touch today and see what options and approaches are available.