ULMA gears up for a boost in service contracts
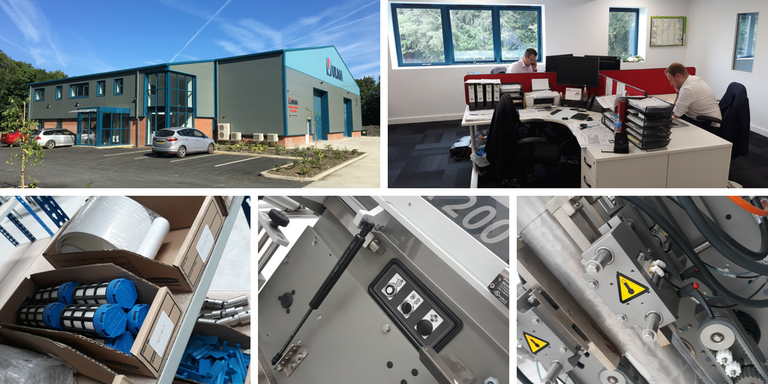
Following a significant increase in service contracts, ULMA Packaging UK has grown its service engineering team to provide extra cover in the UK and Ireland and further reduce the risk of production downtime.
Joe Ribeiro has been appointed as area service manager, Loyd Kingsbury is promoted to automation technician, while Tom Burman is recruited in the role of service technician. The trio will be situated in strategic geographical locations with the aim of providing customers with a a rapid response whenever called upon, anywhere in the country.
ULMA Packaging UK has grown its turnover significantly during the last five years and an increase in service contracts has contributed to that success. The impressive business growth has also led to moving the operation of its UK headquarters to a larger, state of the art premises where even more stock and spare parts can be held and then quickly dispatched. The purpose-built building also conducts equipment trials on new products or films - providing an additional centre of expertise and support for both engineers and customers.
Contracts now account for 20% of service business in the UK and this proportion is growing as customers recognise the value of having full qualified engineers on demand to regularly maintain their equipment under a clever traffic light system that highlights areas of concern and potential future component failures. A 24/7 line to report faults out of hours is also made available to all service customers for extra reassurance and peace of mind.
Part of a co-operative, ULMA Packaging UK is proud of its worldwide reputation for friendly, flexible customer-focused after sales service. Having more boots on the ground is key to making the case for service contracts to accompany systems that are purchased, according to Iain Rae, Service Manager for ULMA Packaging UK.
Iain commented: "A long-term service contract with ULMA Packaging UK means always having frequent contact with dedicated engineers who are proactive and production focused. We are therefore developing our customer care and service techniques in partnership with our customers to optimise performance and training, as well as support process improvements and products evolution in our lines.
"We also take great pride in listening to our customers and acting on their feedback to create packaging solutions that meet their needs now and in the future, which includes in-house repeat training as require."
In addition to basic training, ULMA's service engineers are regularly seconded to the company's main manufacturing site in Onati, Spain. During visits to the site, team members spend time at the technology centre where they are briefed on new industry developments and can familiarise themselves with a customer's equipment during the building process.
ULMA's unique portfolio of thermoforming, traysealing, flow-wrapping, vertical form fill seal and stretch wrapping machines - coupled with the dedicated Automation Division - ensure that each customer has access to the very latest and best in packaging and automation technology.
An approved supplier to multiple retailers and small businesses alike, ULMA Packaging UK now not only has the biggest range of packaging solutions available anywhere in the country, but is leading the way in service contracts that can be tailored to meet customers' needs.
ULMA Packaging is a world leader in the development of innovative packaging solutions. With a choice of over 70 different machine variants, it is represented in more than 40 countries through its own subsidiaries and a global network of highly trained distributors. ULMA Packaging UK is part of the ULMA Group which is made up of co-operatives dedicated to supporting society.
Working on an integral packaging solution, ULMA Packaging UK provides a consistent high-quality service and technical support around the world. This enables larger customers to enjoy the same equipment and care levels across the glove from the UK to Australia and all locations in between.