ULMA PRESENTS MARKET-LEADING MEAT PACKAGING RANGE
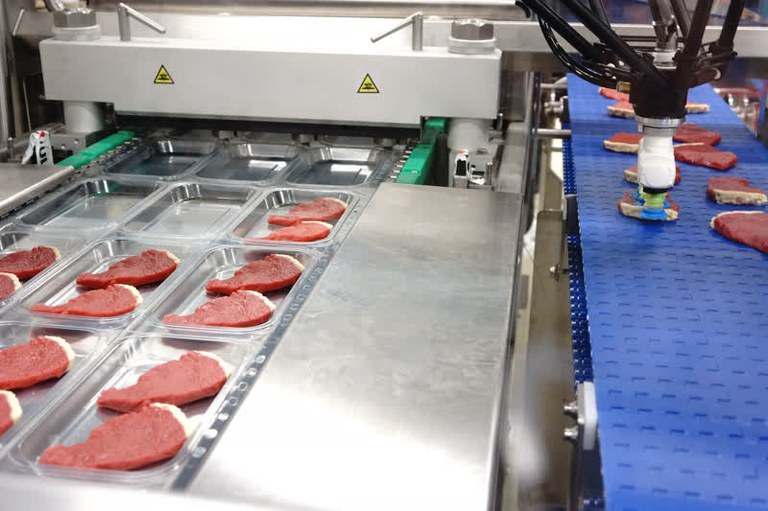
For meat processors, success can hinge on their choice of packaging machinery, and its ability to consistently provide high-integrity, quality packs, shift after shift and year after year.
Consequently, it is vital that stakeholders in the meat industry audit their packaging operations and work closely with machinery operators to ensure best possible performance. This is especially the case as goods and energy prices continue to rise and supply chains remain strained. Additionally, processors across the supply chain must react to sustainability moving from a preference to a priority.
Of all suppliers in the packaging industry, ULMA Packaging (ULMA) stands out for its ability to provide the widest variety of machinery suiting all applications and products. With over 60 years’ experience and representation in over 130 countries, ULMA offers a unique proposition as a Spanish based co-operative.
Traysealing
Key to ULMA’s success is its employment of product specialists dedicated to different sectors, including the meat industry. This approach has enabled the company to develop cutting-edge innovative packaging solutions to processors, including its market-leading traysealing range.
With all models made of stainless steel in a closed-frame design, ULMA’s traysealers are durable, practical and high-performing, while being flexible for format changes and adaptable to different packaging systems. The range’s smooth surfaces limits dirt build-up, making cleaning easier, and all models achieve the IP65 rating as standard. The electrical cabinet is wash-down compliant and easily accessible for maintenance, while belt cleaning and changing can be done without tools, further enhancing practicality.
The compatibility of ULMA traysealers with multiple mediums, including polyester, carton, cardboard and aluminium, also means it is well-placed for meat processors looking to cut down on plastic use. ULMA’s LeafSkinTM and LeafMapTM –green packaging solutions developed under ULMA’s #ULMAweCare sustainability initiative – is compatible with this machinery range. Using a 100% recyclable flat cardboard tray incorporating an ‘easy open’ corner to remove the lid and a ‘recycling’ corner to separate the different materials and make the recycling process easier, LeafSkinTM allows for plastic reductions of up to 80%.
ULMA’s traysealers utilise their continuous motion control synchronisation system that feeds trays continually, making them the fastest on the market. By using gentle and progressive movements, the control ensures maximum product stability and accurate positioning of trays in the sealing area. This allows for throughputs of up to 300 trays per minute at a cadence of 25 cycles/pm with sealing and cutting, and 20 cycles/pm using vacuum or MAP.
Thermoforming
ULMA’s thermoformers for the meat processor market are designed to perform to the most stringent food hygiene requirements. Alongside this, the company can provide turnkey solutions of bespoke design with automatic loading and unloading, ensuring best possible packaging speed and efficiency.
Thermoforming machinery is compatible with multiple packaging methods, including vacuum and MAP methods, and skin packs or even bespoke shapes. For example, the latest of ULMA’s thermoforming solutions, the TFS 216, has been designed to pack products in the sustainable LeafSkinTM format or with LeafMapTM, a further #ULMAweCare solution creating similar material savings to LeafSkinTM in sliced meat packaging. Similarly, the TFS 216 provides a zero-scrap solution, markedly reducing waste.
Flow wrappers
Highly popular across the meat processing sector, flow wrapping machine technology is constantly being updated. ULMA has used its years of knowledge and experience in the poultry industry to develop the new FM 300C machine, building on the strengths of its previous ARTIC C model. The upgraded machine offers improved hygiene, performance and delivers a greater user interface with the myULMA HMI.
Technical innovation in ULMA’s flow wrapper range means further sustainability and efficiency gains can be made regardless of product size. For example, the company has developed installation designs allowing the removal of plastic trays in minced meat packaging. This innovation, which uses MAP, enables processors to make substantial material savings while also protecting products with no discolouration, leakage or compromise on shelf life.
Verticals
Vertical packaging machines are often used to package frozen products such as mince and sausages; as well as fresh items including chicken pieces, legs, wings and thighs. Applicable for frozen items and also compatible with the MAP method for cooked and fresh-to-eat items, a key benefit of this range is that they can pack both naked and marinated products, and powder can even be dropped into the pack so meat can marinate in transit to the customer. ULMA offers a wide range of machinery with intermittent and continuous motion options available, depending on the solution.
With sustainability an industry priority, ULMA has developed the tight bag air extraction method, where air is extracted from bags using a patented jaw arrangement in the cross-seal area. Consequently, meat processors can save on overall onward costs and emissions as products can be packed more efficiently.
An additional benefit of this packaging method is that it avoids contamination issues associated with adding perforations to bags – a previous, popular method of removing excess air. While effective, this hole-punching method can result in products becoming tainted if stored for long periods, as even micro-perforations may lead to humidity loss and possible ingress from external contaminants. Alongside this, the tighter bag caused by air extraction means products have less room to move around in transit, reducing the possibility of potential damage.
ULMA can offer an IP66 upgrade on most models, creating an even more hygienic design. Furthermore, the machine’s forming tube can be changed from the side, making a product change over or carrying out regular hygiene much safer and easier.
Automation
With the energy crisis and rising goods prices continuing to affect all industries, making operations more efficient has never been more pressing. Further compounding this is the availability of cost-effective labour in the UK meat industry. Taking these pressures into account, automation remains an attractive option for processors, especially as technology has advanced in production environments.
Subsequently, ULMA Packaging’s unique ability to leverage the skillsets of partner companies within the global ULMA organisation makes it well-placed to offer complete automation end-of-line processes alongside its machinery offering. This encompasses multiple options, including case erectors, case distribution and logistics, automatic loading equipment, quality control and case packing.
These options are multi-format and distribute packed boxes through a transport system to the end of the packaging line, even when this is located on another factory floor. End-of-line operations can be further automated with robot-based case packers, removing the need for manual handling.
myULMA and UPC
Packaging machine performance remains an ongoing priority for meat processors throughout its lifetime, which is why ULMA has taken steps to ensure its packaging solutions are as intuitive as possible. All solutions are equipped with ULMA’s proprietary UPC control system that provides machine performance data onscreen through a simple, intuitive and configurable HMI.
Additionally, using the myULMA platform, operators can access full technical manuals, order parts, receive remote support and training videos onscreen for instructions on using, maintaining and cleaning the machine. This unique feature helps ULMA stand out from the crowd.
In Conclusion…
The meat processing industry is under pressure to work as efficiently as possible while continuing its progress to more sustainable operations. As a vital part of meat’s journey from the farm to the shelf, packaging processes can always be improved and new packing methods developed.
However, to do so, meat industry stakeholders must work closely with packaging machinery suppliers to identify the most effective systems from both a capex and opex perspective. ULMA’s status as the supplier of the UK’s most extensive choice of packaging machinery means its experts are well-placed to advise meat processors on their packaging machinery needs.